The following case study illustrates one role that materials scientists and engineers are called upon to assume in the area of materials performance: analyze mechanical failures, determine their causes, and then propose appropriate measures to guard against future incidents.
The failure of many of the World War II Liberty ships[1] is a well-known and dramatic example of the brittle fracture of steel that was thought to be ductile.[2] Some of the early ships experienced structural damage when cracks developed in their decks and hulls. Three of them catastrophically split in half when cracks formed, grew to critical lengths, and then rapidly propagated completely around the ships’ girths. Figure shown below is one of the ships that fractured the day after it was launched.
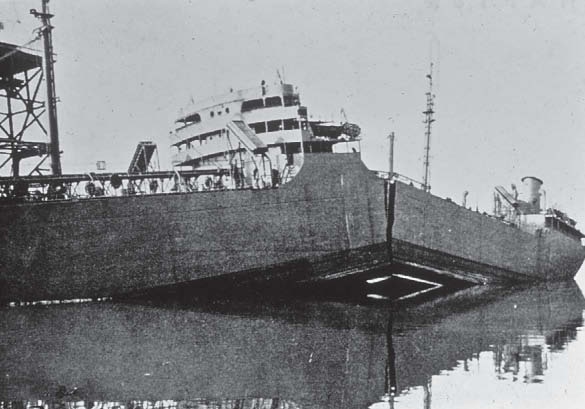
The Liberty ship S.S. Schenectady, which, in 1943, failed before leaving the shipyard. (Reprinted with permission of Earl R. Parker, Brittle Behavior of Engineering Structures, National Academy of Sciences, National Research Council, John Wiley & Sons, New York, 1957.)
Subsequent investigations concluded one or more of the following factors contributed to each failure:
- When some normally ductile metal alloys are cooled to relatively low temperatures, they become susceptible to brittle fracture—that is, they experience a ductile-to-brittle transition upon cooling through a critical range of temperatures. These Liberty ships were constructed of steel that experienced a ductile-to-brittle transition. Some of them were deployed to the frigid North Atlantic, where the once ductile metal experienced brittle fracture when temperatures dropped to below the transition temperature.[3]
- The corner of each hatch (i.e., door) was square; these corners acted as points of stress concentration where cracks can form.
- German U-boats were sinking cargo ships faster than they could be replaced using existing construction techniques. Consequently, it became necessary to revolutionize construction methods to build cargo ships faster and in greater numbers. This was accomplished using prefabricated steel sheets that were assembled by welding rather than by the traditional time-consuming riveting. Unfortunately, cracks in welded structures may propagate unimpeded for large distances, which can lead to catastrophic failure. However, when structures are riveted, a crack ceases to propagate once it reaches the edge of a steel sheet.
- Weld defects and discontinuities (i.e., sites where cracks can form) were introduced by inexperienced operators.
Remedial measures taken to correct these problems included the following:
- Lowering the ductile-to-brittle temperature of the steel to an acceptable level by improving steel quality (e.g., reducing sulfur and phosphorus impurity contents).
- Rounding off hatch corners by welding a curved reinforcement strip on each corner.[4]
- Installing crack-arresting devices such as riveted straps and strong weld seams to stop propagating cracks.
- Improving welding practices and establishing welding codes.
In spite of these failures, the Liberty ship program was considered a success for several reasons, the primary reason being that ships that survived failure were able to supply Allied Forces in the theater of operations and in all likelihood shortened the war. In addition, structural steels were developed with vastly improved resistances to catastrophic brittle fractures. Detailed analyses of these failures advanced the understanding of crack formation and growth, which ultimately evolved into the discipline of fracture mechanics.
Source: Materials Science and Engineering – An Introduction — 9th Edition [Callister & Rethwisch]
References:
[1] During World War II, 2,710 Liberty cargo ships were mass-produced by the United States to supply food and materials to the combatants in Europe.
[2] Ductile metals fail after relatively large degrees of permanent deformation; however, very little if any permanent deformation accompanies the fracture of brittle materials. Brittle fractures can occur very suddenly as cracks spread rapidly; crack propagation is normally much slower in ductile materials, and the eventual fracture takes longer.
[3] This ductile-to-brittle transition phenomenon, as well as techniques that are used to measure and raise the critical temperature range.
[4] The reader may note that corners of windows and doors for all of today’s marine and aircraft structures are rounded.